Introduction
The devastating Palisades and Eaton fires in Los Angeles have left many families displaced, forcing the need to rebuild from the ground up. In response, there is an urgent need to construct homes that exceed current fire safety standards, ensuring greater resilience against future wildfires. While we await code changes, we can get ahead of the curve by designing and building to higher standards. Let’s consider Type III construction with a 2-hour rated roof structure to double the fire resistance rating that was required as part of the City and County’s Type V single family residential standards.
At Letter Four, we provide a truly in-house design-build model, where our architects and contractors work collaboratively to develop fire-resistant construction solutions tailored to your needs. Unlike traditional design-bid-build project delivery models, where homeowners need to work with separate architecture and construction firms, our seamless approach allows us to integrate innovative fireproofing materials and advanced construction techniques from the start to exceed code requirements for single-family homes.
Choosing Letter Four means choosing a team that understands the intricacies of fire-rated roof structures, CMU block wall integration, and advanced fire-resistant materials. Our commitment to safety and superior craftsmanship sets us apart. If you’re rebuilding after a fire, now is the time to incorporate state-of-the-art fire protection into your home’s design. Book a consultation today to discuss how we can help you create a durable, fire-resistant home that protects your family and investment.
This article is primarily technical and not necessarily geared for homeowners, but we’re sharing it anyway. For more details on your rebuilding options and how to best be prepared for your project, take a look at our other articles.
Understanding Fire Resistance Ratings
A fire-resistance rating measures how long a building assembly (such as a wall, floor, or roof) can withstand exposure to fire while maintaining its structural integrity. These ratings are determined through standardized fire testing procedures conducted by organizations such as ASTM, UL (Underwriters Laboratories), or the International Code Council (ICC).
For roof assemblies, fire ratings depend on:
- Structural Elements – Beams, trusses, and decking materials.
- Fireproofing Materials – Fire-resistant coatings, insulation, and underlayment.
- Roof Coverings – External layers such as shingles, metal panels, or membranes.
Achieving a 2-hour fire rating typically involves increasing material thickness, using non-combustible or fire-resistant materials, and incorporating fireproofing layers.
Roof Structural Elements for a 2-Hour Fire Rating
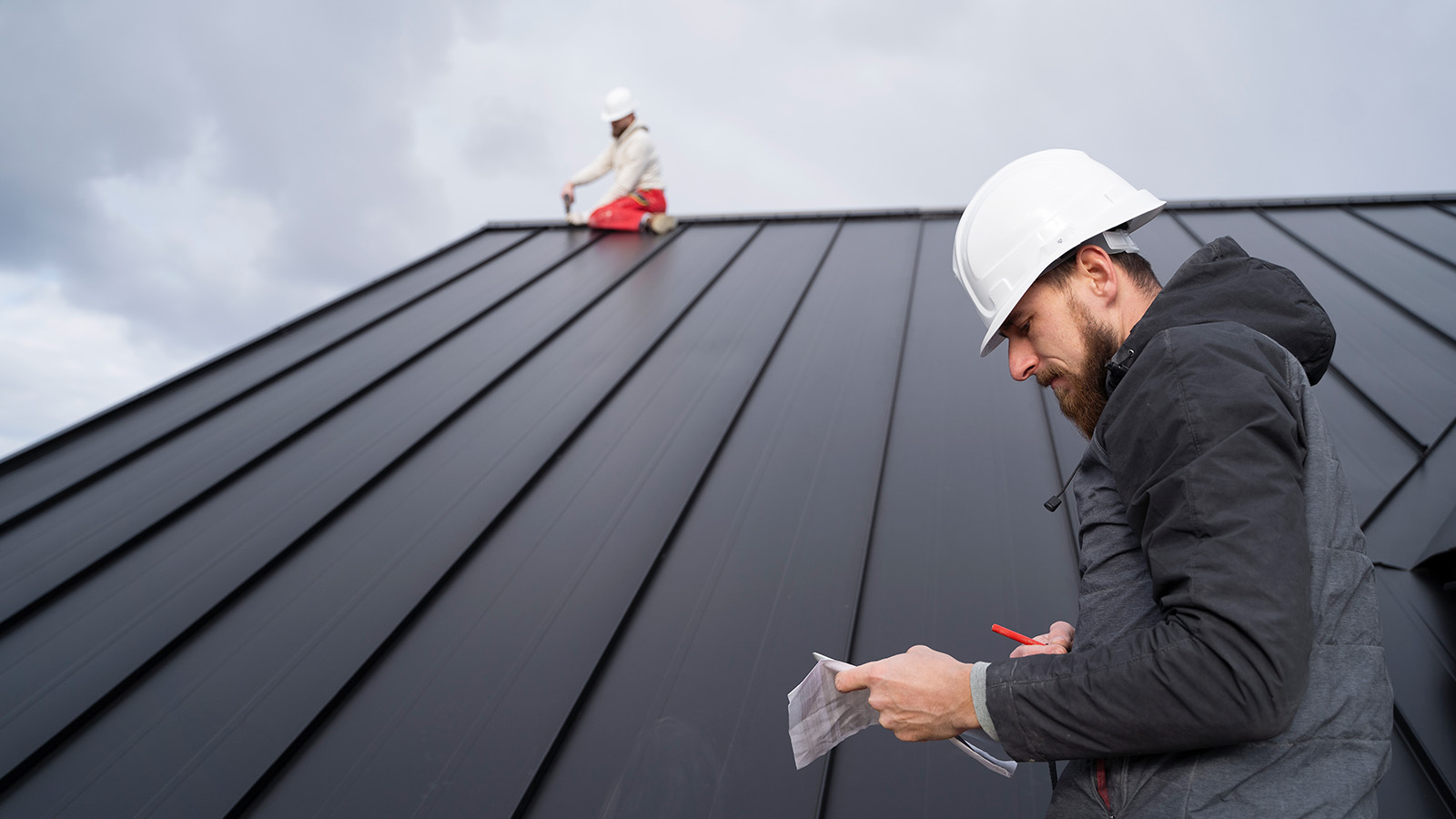
1. Heavy Timber or Fire-Rated Engineered Wood
- Glulam beams and cross-laminated timber (CLT) can achieve a 2-hour rating when properly dimensioned.
- CLT panels should be at least 5-ply (approximately 6.875 inches thick).
- Solid-sawn heavy timber members may require additional fire-retardant treatments or gypsum board encasement.
2. Steel Joists and Girders with Fire Protection
- Unprotected steel fails quickly in fire conditions. To achieve a 2-hour rating, steel components must be coated with intumescent paint, fireproofing spray, or encased in gypsum board or concrete.
- UL-tested assemblies may include 3/8-inch sprayed fire-resistive material (SFRM) or a 2-inch concrete cover over steel elements.
3. Concrete Decking Systems
- Precast concrete panels or cast-in-place concrete slabs offer natural fire resistance.
- 6-inch-thick lightweight or normal-weight concrete can typically provide a 2-hour rating without additional fireproofing.
4. Fire-Rated Wood Trusses
- Type III construction allows for fire-retardant-treated wood (FRTW) trusses, which can meet fire code requirements.
- Trusses must be enclosed with double layers of 5/8-inch Type X gypsum board to reach a 2-hour rating.
Roof Assembly Layers for a 2-Hour Fire Rating
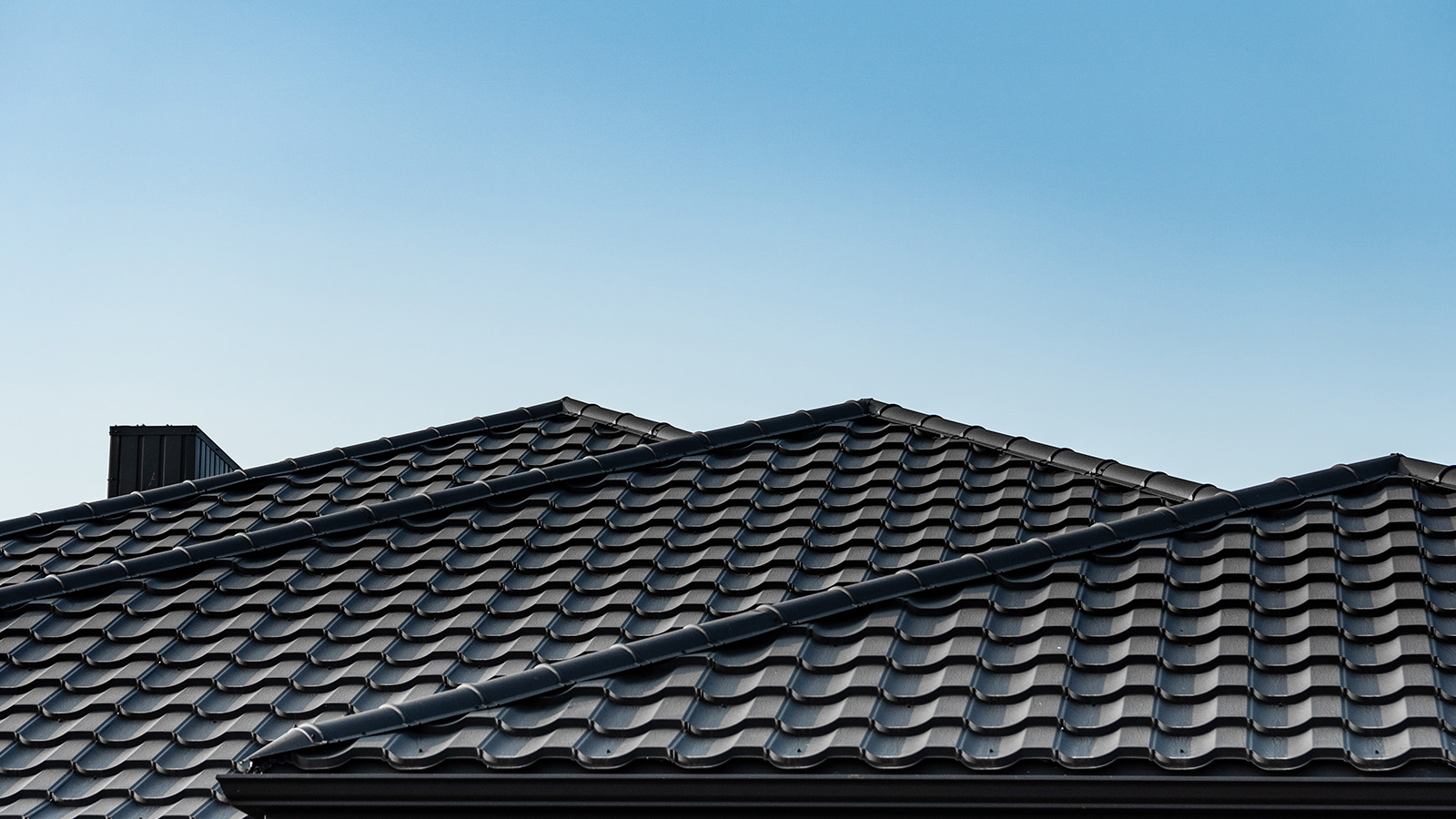
1. Gypsum Board Layering
- Two layers of 5/8-inch Type X gypsum board attached to the ceiling provide significant fire resistance.
- Gypsum board should be installed with staggered joints and secured with fire-resistant sealant.
2. Fire-Retardant Sheathing
- Fire-rated plywood or FRTW sheathing (meeting ASTM E84 or UL 723 standards) enhances fire resistance.
- 3/4-inch fire-retardant-treated (FRT) plywood can contribute to a 2-hour rating when used in conjunction with other materials.
3. Insulation as Fire Protection
- Mineral wool insulation is preferable over standard fiberglass due to its higher melting point.
- Spray-applied fire-resistant materials (SFRM) provide additional passive fire protection, often used in conjunction with steel structures.
4. Fire-Resistant Roofing Membranes
- Single-ply membranes such as EPDM, TPO, or PVC should be Class A fire-rated when tested per ASTM E108.
- Multi-layer built-up roofing (BUR) systems with fire-resistant cap sheets enhance fire performance.
5. Concrete or Lightweight Concrete Topping
- A 2-inch lightweight concrete layer over a metal deck can significantly improve fire resistance.
- This method is often used in commercial or multi-family structures to meet fire-resistance requirements.
Building a 2-Hour Rated Roof for a Single-Family Residence with CMU Block Walls
To achieve a 2-hour fire-rated roof in a single-family residence with CMU block walls, the roof assembly must incorporate non-combustible materials and robust fire-resistant construction techniques. The best approach involves using precast or cast-in-place concrete slabs for the roof deck, which naturally provide a 2-hour fire rating. Alternatively, a steel deck with a 2-inch concrete topping can be used, reinforced with fireproofing spray or intumescent coatings. The underside of the roof should be lined with two layers of 5/8-inch Type X gypsum board, securely fastened to a metal or FRTW framework to prevent flame penetration. Mineral wool insulation should be installed between framing members to enhance thermal protection. The roof membrane should be a Class A fire-rated system, such as a multi-layer BUR or fire-resistant single-ply membrane. Properly sealing all penetrations and junctions with fire-rated caulking ensures that fire cannot breach weak points in the assembly. By combining these strategies, a 2-hour fire-rated roof can be successfully integrated into a CMU block-walled home, enhancing fire resilience and structural integrity.
Architects and engineers must carefully select materials that comply with code requirements, while builders must ensure proper installation practices.
By implementing the above strategies buildings can significantly enhance fire resistance and safety, ultimately protecting occupants and property against fire hazards. For more information on your options for rebuilding, refer to this resource.