Rebuilding after devastating wildfires in Los Angeles, Malibu, Altadena, and Pasadena is no small task, and there is much to do to help our communities recover and prepare to build back stronger. Clearing sites and removing hazardous materials are critical first steps toward creating a foundation for safe and resilient new homes.
The recent wildfires in the Los Angeles area have further exposed vulnerabilities in local housing stock and emphasized the need for more resilient construction practices. These fires have been fueled by climate change, urban sprawl, and natural conditions unique to California’s environment. Most homes in these areas, built with Type V construction methods, are particularly susceptible to fire damage. As rebuilding efforts begin, it’s crucial to consider alternative construction methods, such as Type III construction, which offers significantly enhanced fire resistance.
So Why Are We Proposing Type III Construction For Single Family Homes and Not Something More Innovative?
Type III construction strikes the right balance between proven performance, practicality, and accessibility. While there are more innovative building methods and materials available, many of these solutions are still emerging, come with higher costs or special testing and approvals, or lack the widespread expertise needed for large-scale adoption. Type III construction, on the other hand, has been around for decades and is a tried-and-true approach that architects, builders, and inspectors are already familiar with. It’s a common method for multi-family housing, meaning the transition to using it for single-family homes is both feasible and efficient. By leveraging a system that’s already well understood and scalable, we can rebuild safer, more fire-resistant homes without introducing unnecessary complexity or delays, ensuring our communities are ready to move forward confidently.
And Why Are We Still Building Homes primarily with Wood here in Los Angeles?
Watch this video for a quick explanation.

The City of Los Angeles has long facilitated the use of Type V construction for single-family homes, prioritizing simplicity and accessibility in the permitting process. A designer—who does not need to be a licensed architect or structural engineer—can submit plans and secure permits by following the prescriptive guidelines outlined in a standardized handout from the Los Angeles Department of Building and Safety (LADBS). This approach streamlines approvals but often results in homes built with lightweight wood framing, a material highly vulnerable to fire. While this process is efficient and cost-effective, it also underscores the need for more fire-resistant construction methods, especially in wildfire-prone areas.
In this article, we’ll share key strategies for rebuilding safer, more fire-resistant homes, with the goal of protecting not just individual properties but entire communities.We’ll define the different types of construction, compare Types III and V, and explore how Type III construction can improve fire resilience. We’ll also dive into the importance of fire assembly ratings, recommended materials and designs, and holistic strategies like defensible space and fire-adaptive landscaping.
If you need and want to rebuild, we want you to know that Letter Four is here for you. We’re committed to being proactive in providing resources, research, and guidance to help you design and build with wildfire resilience in mind.
Understanding Construction Types and Fire Resistance
Construction Types Defined
The International Building Code (IBC) categorizes buildings into five main construction types based on the combustibility and fire-resistance of materials used:
- Type I (Fire-Resistive): Constructed with non-combustible materials such as concrete and steel, with the highest fire resistance ratings.
- Type II (Non-Combustible): Similar to Type I but with less stringent fire-resistance requirements.
- Type III (Ordinary Construction): Combines non-combustible exterior walls (e.g., masonry or concrete) with combustible or limited combustible interior elements.
- Type IV (Heavy Timber): Utilizes large-dimension wood members with inherent fire resistance due to their slow burn rate.
- Type V (Wood Frame): Predominantly wood construction, with little to no fire-resistance rating, making it the least fire-resistant type.
Type III vs. Type V Construction
Type V construction is commonly used for single-family homes due to its affordability, ease of construction, and design flexibility. However, its reliance on lightweight wood framing makes it highly vulnerable to ignition and structural failure during wildfires.
In contrast, Type III construction uses non-combustible materials for exterior walls, such as concrete or masonry, which are far more resistant to fire. While it may incorporate some combustible materials in the interior, the design mitigates fire spread from external sources—a critical factor in wildfire-prone areas.
Type III construction incorporates 2-hour rated exterior walls. Let’s dive into fire assembly ratings below:
Fire Assembly Ratings and Their Importance
What Are Fire Assembly Ratings?
Fire assembly ratings measure the ability of a building component (walls, floors, roofs) to resist fire penetration for a specified time, often expressed in hours (e.g., a 2-hour rating). These ratings are determined through standardized testing and are vital for slowing fire spread and providing occupants with time to evacuate.
Why a 2-Hour Exterior Wall Is Better
We’re clearly stating the obvious, by noting that a 2-hour fire-rated exterior wall can withstand fire exposure twice as long as a 1-hour wall. This extended resistance:
- Prevents ignition from radiant heat or embers.
- Reduces the likelihood of structural failure.
- Provides critical time for firefighting efforts and evacuation.
In wildfire scenarios, where embers can ignite homes from miles away, the enhanced protection of a 2-hour-rated wall can make the difference between survival and destruction.
Recommended Materials and Systems for Type III Construction
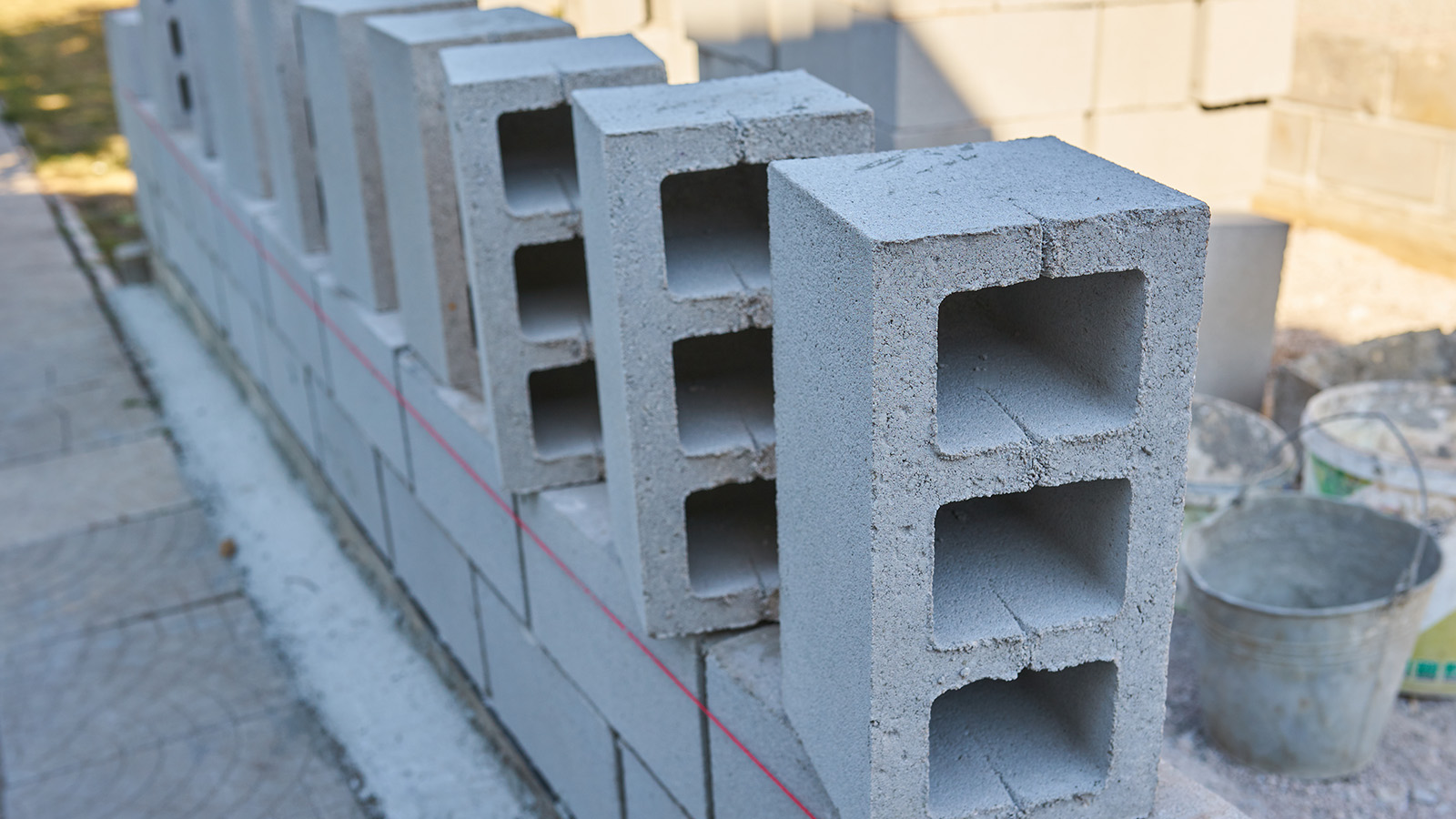
Exterior Wall Assemblies
To achieve a 2-hour fire rating, consider the following wall assemblies:
- Concrete Block or Insulated Concrete Forms (ICFs): Non-combustible and thermally stable, these systems provide excellent fire resistance.
- Fire-Resistant Gypsum Board: Layers of Type X or Type C gypsum board can be added to enhance fire resistance.
- Fiber Cement Siding: Combines durability with non-combustibility, making it a top choice for exterior finishes. Keep in mind that what matters most here is the full wall assembly, not just the exterior finish.
- Stucco: ⅞” stucco over a fire-resistant wall construction is highly non-combustible. If you like the look of stucco it can also be used as a “skim coat” over concrete block or ICF’s to achieve the 2-hour rating.
In the Los Angeles area, stucco over wood framing is a common exterior wall assembly for single-family homes and it only provides a 1-hour fire rating. This assembly relies heavily on the thickness of the stucco and the fire resistance of the underlying wood framing. As highlighted in this article on stucco’s fire performance, stucco itself is non-combustible and can withstand high temperatures, but its fire-resisting capabilities are dependent on the materials behind it.
To achieve a 2-hour fire rating with stucco, modifications to the standard assembly are necessary. For those rebuilding in very high fire severity areas, combining a stucco exterior with a more robust fire-resistant assembly or opting for non-combustible materials like concrete or masonry may offer better protection.
Roofing Systems
Roof assemblies are critical in wildfire resilience:
- Class A Roofing Materials: Options like asphalt shingles, clay tiles, and metal roofs provide the highest fire resistance.
- Continuous Roof Decking: Minimizes gaps where embers can enter.
- Gutter Guards: Prevent debris accumulation that can ignite from embers.
Type III construction typically requires a 1-hour rated roof assembly, meaning the roof system is designed to resist fire exposure for at least one hour before it compromises the structure. However, in very high fire severity zones—like those impacted by the recent wildfires in Los Angeles, Malibu, Altadena, and Pasadena—we strongly recommend using a 2-hour rated roof assembly for added protection.
In simple terms, a 2-hour rated roof assembly is a roof built with materials and layers that can withstand fire for two hours without allowing flames to penetrate into the home. This extended time provides a critical buffer during a wildfire, helping protect the structure from ember storms and radiant heat, which are common causes of roof ignition.
A 2-hour rated assembly typically includes:
- Non-combustible or fire-resistant materials like metal or concrete tiles.
- Multiple protective layers, such as a fire-resistant underlayment and insulation.
- Specialized design details that prevent embers from entering through vents or gaps.
Eave and Vent Details
Eaves and vents are some of the most vulnerable to ember entry. Innovative eave and roof vent products are transforming wildfire resilience. Mitigation strategies, details, and products include:
- Boxed Eaves: Enclose eaves with fire-resistant materials to prevent ember entry. This is already a code requirement here in LA, in areas with High and Very High Fire Severity designations.
- Vented Soffits with Mesh: Use 1/8-inch metal mesh to block embers while allowing airflow.
- Ridge Vents: Opt for fire-rated ridge vent systems designed to resist ember penetration.
Many of these products incorporate fine metal mesh or intumescent materials that expand when exposed to heat, sealing off the vent openings during a fire. In the City of Los Angeles, such products typically need to meet strict performance testing requirements, including obtaining an LARR# (Los Angeles Research Report number), which certifies that they comply with local building codes. Additionally, products must demonstrate effectiveness through wildfire-specific testing, such as the ASTM E2886 standard, which evaluates ember resistance.
Slab-On-Grade Foundations
In wildfire-prone areas, slab-on-grade construction is preferred over raised floor systems due to its inherent fire resistance and reduced vulnerability to embers. A slab-on-grade foundation involves pouring a solid concrete slab directly onto the ground, eliminating the crawl space found in raised floor construction. Crawl spaces are susceptible to ember intrusion and the accumulation of combustible debris, which can ignite and compromise the home’s structural integrity during a wildfire. Additionally, concrete is non-combustible and provides a solid barrier against ground-level fires. This makes slab-on-grade a safer and more resilient choice for homes in high fire risk zones. For more information on the advantages of slab-on-grade construction in fire-prone areas, check out this article from the Insurance Institute for Business & Home Safety (IBHS).
Fire Suppression Systems
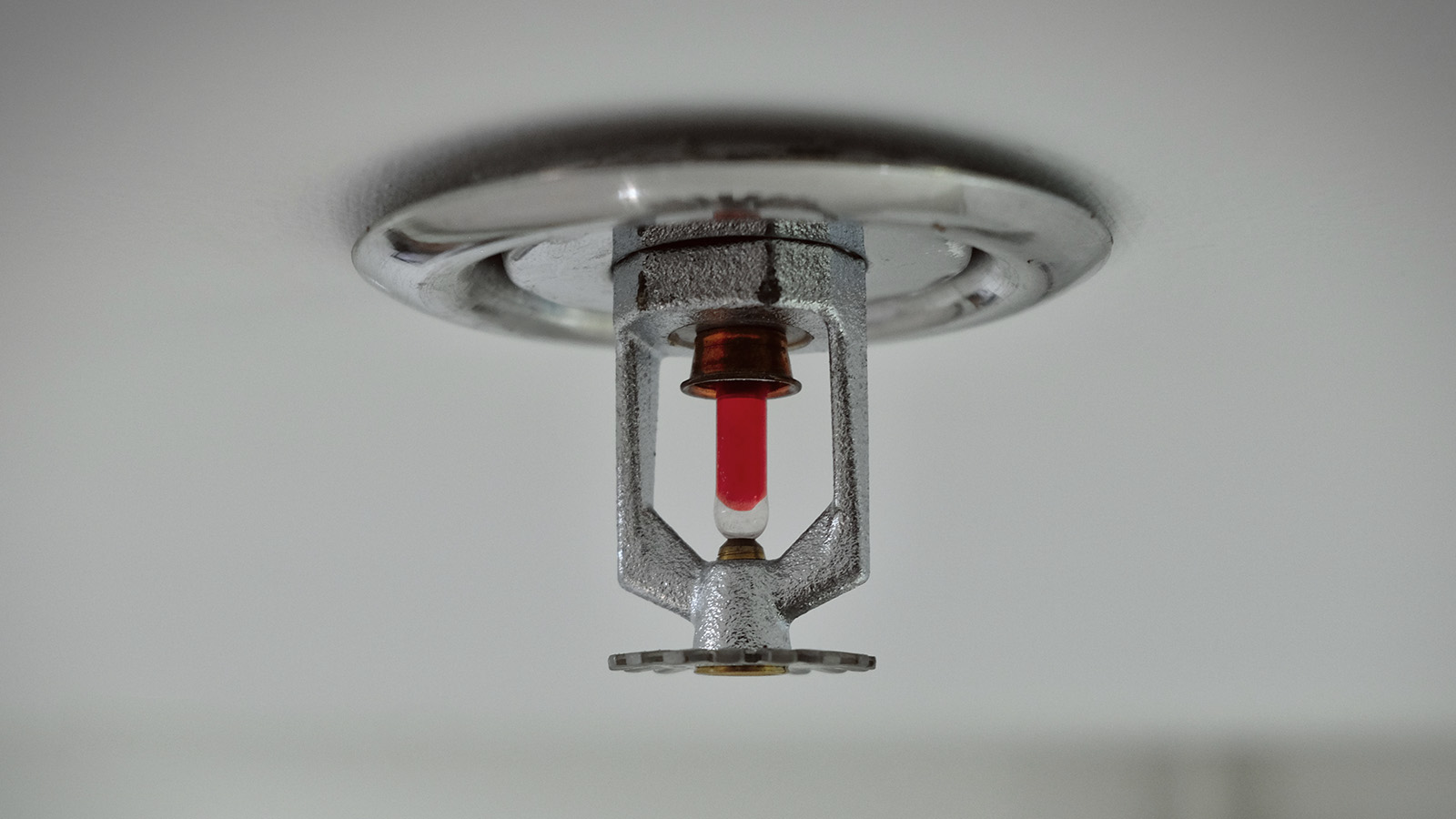
Fire suppression systems are a critical component of wildfire-resilient homes, offering both interior and exterior protection against fire spread. Interior fire sprinklers, now required by code for new single-family residential homes, are designed to activate when heat from a fire reaches a specific threshold, releasing water to suppress flames and prevent further damage. Unfortunately, many of the homes that burned in the recent wildfires were built before this requirement and lacked this vital safety feature. Exterior fire suppression systems, such as rooftop-mounted sprinklers or perimeter water spray systems, can also provide a first line of defense against embers and radiant heat during a wildfire. These systems help to keep exterior surfaces cool and moist, reducing the likelihood of ignition. For homes in high-risk areas, combining interior and exterior fire suppression systems with other fire-resilient measures, like defensible space and non-combustible materials, is essential for maximizing safety and reducing potential losses.
Landscaping and Defensible Space
Zone 0: The Immediate Non-Combustible Zone
Zone 0 extends 0-5 feet from the structure and should be entirely free of combustible materials. Guidelines from the Insurance Institute for Business & Home Safety (IBHS) recommend:
- Non-combustible ground cover like gravel or pavers.
- Removal of mulch, wood chips, and flammable plants.
- Use of hardscaping to create a fire break.
Defensible Space
Beyond Zone 0, defensible space involves creating a buffer between your home and surrounding vegetation:
- Zone 1 (5-30 feet): Maintain low-growing, fire-resistant plants and prune trees regularly.
- Zone 2 (30-100 feet): Thin vegetation and remove ladder fuels to reduce fire intensity.
Fencing and Site Materials
- Use non-combustible materials like steel or masonry for fencing near the home.
- Avoid attaching wooden fences directly to the house, as they can act as fire conduits.
Wildfire-Resilient Landscaping
Plant Selection
Choose plants with high moisture content and low resin or sap levels, such as succulents, lavender, and ceanothus.
Tree Placement
Maintain a minimum distance of 10 feet between tree canopies and at least 30 feet from the structure. Regular pruning is essential.
Irrigation Systems
Incorporate drip irrigation to maintain plant moisture without excessive water use.
Resources for Wildfire Resilience
As communities across Los Angeles, Malibu, Altadena, and Pasadena rebuild, adopting Type III construction offers a path to greater safety and resilience. By combining non-combustible materials with strategic design and landscaping, homeowners can significantly reduce wildfire risks. While these measures may increase upfront costs, they provide unparalleled peace of mind and long-term savings on things like insurance and maintenance.
Investing in fire-resilient construction is not just about protecting individual homes—it’s about safeguarding entire communities. Let’s build smarter, stronger, and safer together.
To implement these strategies effectively, consult the following resources:
- Letter Four | Post-Fire Rebuild Resources
- Wildfire Resilience Design Strategies for Architects and Homeowners
- Wildfire Preparedness Primer
- Noncombustible Zone 0 Guidelines
- Suburban Wildfire Adaptation Roadmaps
- NFPA: Preparing Homes for Wildfire
- Construction Types and Material Combustibility
- Hardening for Wildfire Resilience
- Arch Daily: The Impact of Wildfires on Building Codes: Reflections on the Recent Los Angeles Fires
How To Get Started on Your Fire Resilient and Resistant Rebuild
Rebuilding a home after a wildfire is a deeply personal and often overwhelming experience. It involves navigating complex decisions, local regulations, and emotional challenges—all while striving to create a safer, more resilient future for your family. In this context, the Design-Build model offers unparalleled benefits by integrating the design and construction processes under a single team, ensuring seamless communication, greater efficiency, and a more personalized experience.
What Is Design-Build, and Why Does It Matter?
The Design-Build approach streamlines the entire process from initial concept to final completion. This contrasts with the traditional Design-Bid-Build method, where homeowners must separately hire an architect and a contractor, often leading to communication gaps, unforeseen delays, and unexpected costs. By choosing Design-Build, you benefit from:
- Single-Point Accountability: One team oversees the project, ensuring clear communication and accountability at every stage.
- Streamlined Timeline: Design and construction processes overlap, reducing project timelines compared to the sequential approach of Design-Bid-Build.
- Cost Transparency: Integrated budgeting minimizes surprises, giving you a clearer understanding of costs upfront. We create an all-in budget at the very start of your project. This includes surveys, design and engineering costs, plan check and permit fees, construction costs, finishes and fixtures, and exterior work like hardscaping and landscaping.
- Collaborative Solutions: Designers and builders work together to address challenges creatively and efficiently.
For wildfire rebuilds, where time, cost, and resilience are critical, Design-Build offers the most effective and cohesive path forward.
How Is Letter Four Unique?
At Letter Four, we’re different from other Design-Build firms. Our team includes truly in-house licensed architects and contractors. Many other firms only say they’re Design-Build, when they’re actually just a contractor who sub-contracts an architect or designer, or has a designer on staff, rather than a licensed architect. In addition to licensed architects and contractors, we also have an in-house Interior Design team as well as a network of engineers, permit expeditors, and subcontractors, who we assemble and coordinate with throughout your project.
We start every project with an Action Plan and maintain frequent, collaborative communication throughout the course of every project with our Clear 4-Step Process. We use BIM software tools to help you to visualize your new home and are custom-developing tools to give you the full picture of your project via your Client Portal, so you always have access to your project schedule, budget, drawings, renderings, finishes and fixtures, and so much more.
Our process is grounded in empathy, expertise, and an unwavering commitment to delivering homes that are as beautiful as they are safe. Here’s how our approach stands out:
1. A Compassionate and Personalized Approach
We understand that rebuilding after a fire isn’t just about constructing a house—it’s about reclaiming your sense of security and belonging. That’s why we prioritize listening to your needs, values, and vision for your home. From the first consultation, we’ll work closely with you to create a design that reflects your lifestyle while incorporating the latest fire-resilient strategies.
Our team is deeply connected to the communities affected by wildfires, and we approach every project with care and compassion. We’re not just your builders—we’re your partners in rebuilding and healing.
2. Expertise in Wildfire-Resilient Design
Wildfire rebuilding requires specialized knowledge of fire-resistant materials, building codes, and defensible space principles. At Letter Four, we stay at the forefront of wildfire resilience by integrating best practices into every design. Our team’s expertise ensures that your home not only meets local codes but also exceeds them, giving you peace of mind in the face of future fire threats.
3. Full Transparency and Accountability
Rebuilding can be a daunting financial commitment, which is why we prioritize transparency at every step. With our integrated team, you’ll receive detailed cost estimates and updates throughout the project, so there are no surprises.
Because we manage both design and construction, we’re able to provide a seamless feedback loop between the two processes. This ensures that design ideas are not only innovative but also practical and cost-effective to execute.
4. Tailored Design for Every Family
Your home is a reflection of your unique needs and lifestyle. At Letter Four, we don’t believe in cookie-cutter solutions. Our team works collaboratively with you to create a design that balances aesthetics, functionality, and resilience. Whether you’re envisioning a modern, minimalist retreat or a warm, traditional family home, we’ll tailor every detail to bring your vision to life.
Are You Ready to Talk About Your Rebuild?
Rebuilding after a wildfire is a journey, but you don’t have to navigate it alone. At Letter Four, we’re here to guide you every step of the way, providing the expertise, compassion, and innovation needed to create a home that’s safe, beautiful, and uniquely yours.
If you’re ready to start rebuilding or just want to learn more about our process, we encourage you to book a call on our Fire Rebuild page today. Visit letterfour.com/fire-rebuild to schedule your consultation and take the first step toward a brighter, more resilient future.