In California, particularly in Los Angeles, wood framing has long been the predominant method for constructing single-family homes. This preference is deeply rooted in the region's history, availability of materials, and economic considerations. However, recent devastating events, such as the Palisades and Eaton fires, have prompted a reevaluation of building practices to enhance resilience against natural disasters.
Why Wood Framing Prevails in California
- Material Availability and Cost: Historically, California has had abundant timber resources, making wood a readily available and cost-effective building material. The extensive forests in the northern part of the state provided a steady supply of lumber, which, coupled with established logging and milling industries, reduced transportation costs and made wood an economical choice for builders.
- Construction Tradition and Skills: The tradition of wood-framed construction dates back to the early settlers and has been perpetuated through generations. This long-standing practice means that the construction workforce is predominantly trained in wood framing techniques, ensuring efficiency and expertise in this method. The familiarity with wood also translates to faster construction times, as builders are well-versed in the nuances of working with this material.
- Building Codes and Regulations: California's building codes have historically been tailored to wood-framed structures. These codes have evolved to address seismic concerns, given the state's earthquake activity, by incorporating requirements for shear walls, bracing, and anchoring specific to wood construction. The existing regulatory framework thus supports and perpetuates the use of wood framing.
- Flexibility and Aesthetics: Wood offers design flexibility, allowing architects and builders to create a variety of styles and adaptations. Its versatility enables modifications and renovations with relative ease, which is appealing to homeowners. Additionally, many find the aesthetic qualities of exposed wood—such as its warmth and natural appearance—desirable in residential construction.
- Economic Factors: The cost-effectiveness of wood, both in terms of material and labor, has made it the preferred choice for single-family homes. The established supply chain and competitive pricing of lumber, combined with a skilled labor force, have traditionally kept construction costs lower than alternative building methods. This is even true during the pandemic, when the cost of lumber skyrocketed.
Fire Hazard Severity Zones in California
The California Department of Forestry and Fire Protection (CAL FIRE) has designated various regions as Very High Fire Hazard Severity Zones (VHFHSZ). These zones are identified based on factors such as fuel load, terrain, and weather patterns. In recent years, the state has updated these designations to reflect the increasing wildfire risks. For instance, more than 80% of new properties in California from 2020 to 2022 were constructed in high fire-risk areas, a significant increase from previous decades.
Los Angeles County, in particular, has numerous areas classified under VHFHSZ. The Los Angeles Fire Department (LAFD) provides resources and maps detailing these zones, assisting homeowners and builders in making informed decisions about construction practices and materials.
Reevaluating Building Practices Post-Fire Events
The Palisades and Eaton fires resulted in significant loss of property and life, underscoring the vulnerability of wood-framed homes to wildfires. These events have catalyzed discussions among policymakers, builders, and homeowners about adopting more fire-resistant construction methods.
Exploring Alternative Construction Types
Building construction is categorized into five types, each with varying degrees of fire resistance and material composition:
- Type I: Fire-Resistive Construction: This type includes high-rise buildings made of non-combustible materials like concrete and protected steel. These structures are designed to withstand high temperatures for extended periods, providing up to four hours of fire resistance.
- Type II: Non-Combustible Construction: Common in newer commercial buildings, Type II structures have walls made of non-combustible materials but may have roofs made of combustible materials. They offer less fire resistance than Type I buildings.
- Type III: Ordinary Construction: Often found in older buildings, this type has non-combustible exterior walls but combustible interior framing. Multi-family residential buildings frequently fall into this category.
- Type IV: Heavy Timber Construction: Characterized by the use of large wooden beams and columns, Type IV construction is known for its robustness and fire resistance due to the sheer size of the timber components.
- Type V: Wood-Framed Construction: The most common type for single-family homes, Type V construction utilizes entirely combustible materials, including wood framing for both interior and exterior walls.
Given the fire risks associated with Type V construction, there is a growing advocacy for transitioning to more fire-resistant types, particularly Type III construction, even for single family residences.
Comparative Analysis: California and Mexico
Interestingly, while California predominantly uses wood framing for residential construction, its neighboring country, Mexico, primarily employs concrete and rebar. This contrast is influenced by factors such as material availability, cultural practices, and historical building codes.
Mexico's preference for concrete construction has resulted in residential buildings that are generally more resistant to natural disasters, including fires and earthquakes. The widespread use of concrete has also fostered a construction industry adept in masonry techniques, with a supply chain optimized for concrete materials.
Shifting the Narrative in California
Transitioning from traditional wood framing to concrete block construction in California requires a multifaceted approach:
- Policy and Building Codes: State and local governments can revise building codes to encourage or mandate the use of fire-resistant materials in high-risk areas. This could involve offering incentives for builders who adopt concrete construction methods.
- Public Awareness and Education: Homeowners and builders need to be informed about the benefits of concrete construction, particularly its fire-resistant properties. Educational campaigns can highlight success stories and provide resources on best practices.
- Training and Workforce Development: Investing in training programs for contractors and construction workers can facilitate the adoption of concrete construction techniques, ensuring a skilled workforce is available to meet increased demand.
- Supply Chain Enhancement: Developing a robust supply chain for concrete materials, including partnerships with local manufacturers, can make concrete construction more accessible and cost-effective.
Benefits of Building with Concrete Blocks
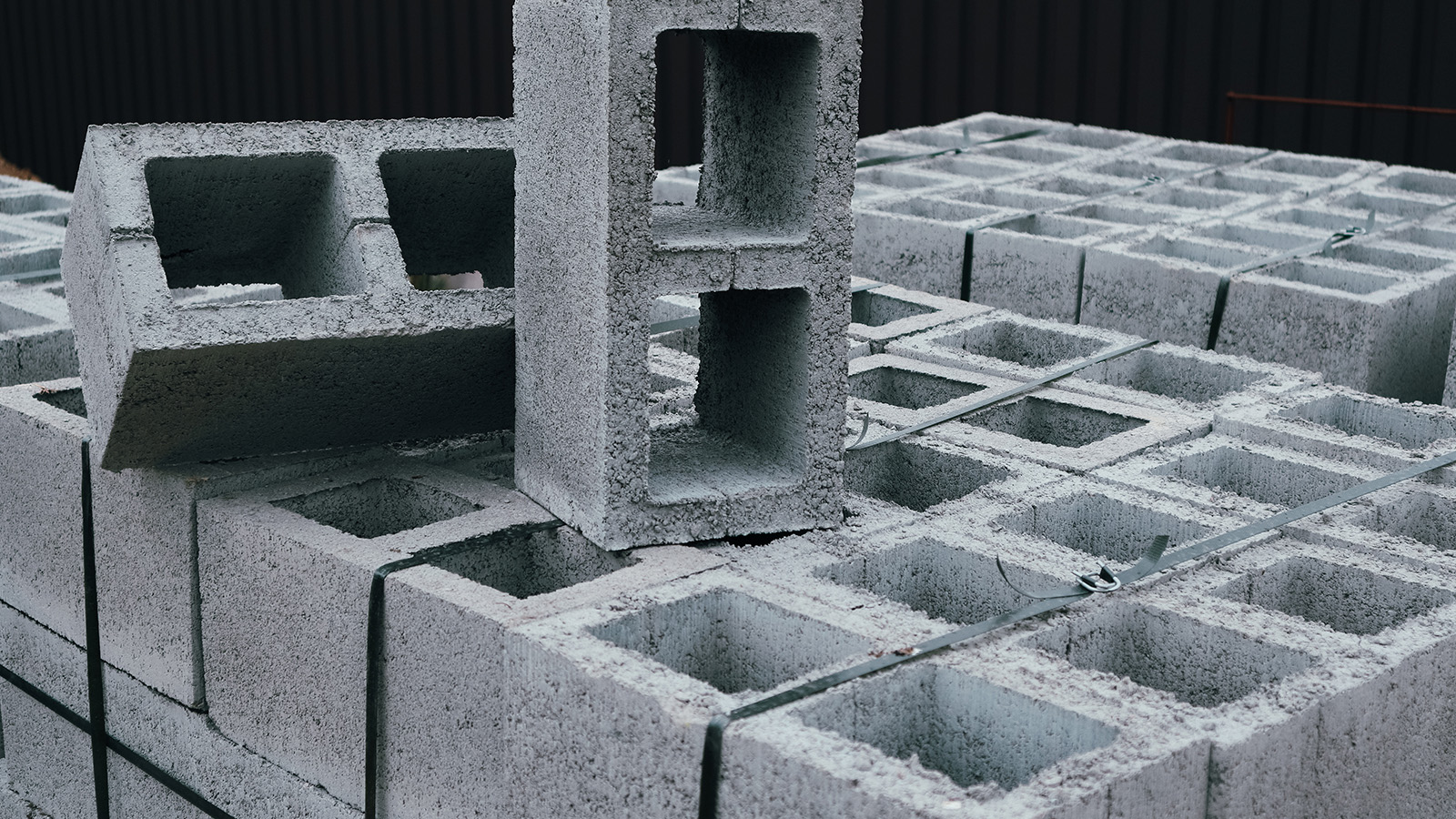
Concrete block construction offers several advantages, especially in fire-prone areas:
- Fire Resistance: Concrete blocks are non-combustible and can withstand high temperatures without losing structural integrity. This characteristic significantly reduces the risk of fire spreading and enhances the safety of the occupants.
- Durability and Strength: Concrete blocks provide robust structural support, offering resistance against natural disasters such as earthquakes and hurricanes. Their strength contributes to the longevity of the building, reducing the need for frequent repairs. The use of steel rebar is required for lateral resistance and structural details are already widely employed for multi-family and mixed used construction in the Los Angeles area and beyond.
- Thermal Efficiency: The thermal mass of concrete blocks helps in maintaining consistent indoor temperatures by absorbing and slowly releasing heat. This property can lead to energy savings in heating and cooling.
- Sound Insulation: The density of concrete blocks offers excellent sound insulation, creating quieter indoor environments by dampening external noise.
- Pest Resistance: Unlike wood, concrete is impervious to termites and other pests that can compromise the structural integrity of a building.
- Low Maintenance: Buildings constructed with concrete blocks require minimal maintenance compared to wood-framed structures, as they are less susceptible to rot, warping, and insect damage.
- Environmental Considerations: Utilizing concrete can reduce the demand for timber, thereby preserving forests and contributing to environmental conservation efforts.
Domestic Production of Concrete Blocks
The United States has a well-established concrete block manufacturing industry. According to a 2025 market research report, there are 433 companies engaged in concrete block and brick manufacturing across the country, with industry sales reaching $6.1 billion in 2024.
Utilizing domestically produced concrete blocks can mitigate the impact of international trade tariffs. Recent policy changes have seen the imposition of tariffs on steel and aluminum imports, with potential extensions to other construction materials. For example, in February 2025, President Trump announced a 25% tariff on steel and aluminum imports, affecting the cost of construction materials.
By sourcing materials from U.S. manufacturers, builders can avoid additional costs associated with tariffs, leading to more predictable budgeting and potentially lower construction costs.
Economic Considerations
The increasing frequency and severity of wildfires in California necessitate a reevaluation of traditional construction practices. Embracing concrete block construction offers a viable path toward building more resilient, durable, and energy-efficient homes. By updating building codes, educating stakeholders, and leveraging domestic manufacturing, California can shift toward construction methods that prioritize safety and sustainability in the face of evolving environmental challenges.
Look at it this way: Type III Construction is nothing new here, it’s just new for single family residential construction. If contractors can work together to build single family homes like we have been building multi-family and mixed use, we can make our city safer for years to come.
While the initial costs of concrete block construction may be higher than wood framing, several factors can offset this investment:
- Insurance Premiums: Homes built with fire-resistant materials like concrete may qualify for reduced insurance premiums, as they present a lower risk to insurers.
- Maintenance and Repair Costs: The durability of concrete reduces the need for frequent repairs and maintenance, resulting in long-term savings for homeowners.
- Energy Efficiency: The thermal properties of concrete can lead to lower energy bills, as homes remain cooler in the summer and warmer in the winter.
- Resale Value: Fire-resistant homes may have a higher resale value, particularly in areas prone to wildfires, as buyers prioritize safety and durability.
A Case Study for Type III Construction
When considering the construction of a 3,000-square-foot single-family home in Los Angeles, the choice between Type III and Type V construction significantly impacts both initial costs and long-term financial considerations. Type III construction, characterized by non-combustible exterior walls and combustible interior elements, is typically employed in mid-rise buildings and necessitates materials like masonry or fire-retardant-treated wood for exterior walls. In contrast, Type V construction allows for combustible materials throughout, commonly utilizing light-framed wood, and is prevalent in smaller residential projects due to its cost-effectiveness and simpler construction methods.
Construction Cost Differences
In Los Angeles, construction costs vary widely based on design, site conditions, materials, and labor. As of recent data, the average hard costs to build an affordable home in Los Angeles starts around $400+ per square foot, though this can fluctuate depending on specific location, choices and market conditions.
Letter Four specializes in custom home design and construction, delivered through our CLEAR 4-Step process. We’re licensed architects and contractors, as well as interior designers and provide a true one-stop-shop for all of your design-build needs. It’s important to note that the construction cost listed above is just that, and falls short of the all-in budget required to rebuild your home. A full rebuild budget needs to include soft costs like architectural and engineering fees, finishes and fixtures, permit costs, and so much more. We also recommend including a contingency in your budget to account for the expected increase in construction costs due to demand and labor and material shortages. We’ve created our Action Plan to provide you with the all-in budget you need to confidently move forward with your rebuild and avoid surprises, delays, and cost overruns.
Type III construction generally incurs higher costs than Type V due to the requirement for non-combustible materials and enhanced fire-resistance features. While precise percentage increases can vary, industry analyses suggest that building with materials like concrete and steel (common in Type III) can be significantly more expensive. For instance, projects utilizing Type I construction (primarily concrete and steel) have been found to cost an average of $65 more per square foot than other types.
Although this data pertains to Type I, it underscores the cost implications of using non-combustible materials.
Applying this to a 3,000-square-foot home, if we consider the lower end of the cost spectrum for Type V construction at $400 per square foot, the total cost would be:
$400/sq ft × 3,000 sq ft = $1,200,000
Assuming Type III construction increases costs by approximately 20% (a conservative estimate based on the need for non-combustible materials and additional fireproofing), the per-square-foot cost would rise to $465, resulting in:
$465/sq ft × 3,000 sq ft = $1,395,000
This reflects an additional $195,000 in construction costs when opting for Type III over Type V.
Insurance Costs
One of the advantages of Type III construction is the potential for reduced insurance premiums. The use of non-combustible materials and enhanced fire-resistance measures decrease the risk of fire damage, which insurers often recognize with lower rates. While specific savings vary, some studies have indicated that buildings with fire-resistive construction can see substantial reductions in insurance premiums over time.
Maintenance and Repair Costs
Type III construction, utilizing materials like masonry and treated wood, often results in structures that are more durable and require less frequent maintenance compared to the all-wood framing of Type V. The initial investment in higher-quality, non-combustible materials can lead to savings in repair and upkeep over the lifespan of the home.
Energy Efficiency
The choice of construction type also influences energy efficiency. Buildings constructed with insulated concrete forms (ICFs), a method comparable with Type III construction, have demonstrated energy savings of 30-40% compared to traditional wood-frame buildings.
These savings are attributed to the superior insulation properties and thermal mass of materials used in Type III construction, leading to reduced heating and cooling costs.
Resale Value
Homes built with Type III construction may command higher resale values due to their durability, enhanced safety features, and energy efficiency. The growing market demand for energy-efficient and resilient homes can make such properties more attractive to buyers, potentially leading to a higher return on investment.
Conclusion
Opting for Type III construction for a 3,000-square-foot home in Los Angeles involves a higher initial investment, estimated at an additional $195,000 for hard costs, compared to Type V construction. However, this upfront cost can be offset over time through savings in insurance premiums, reduced maintenance and repair expenses, improved energy efficiency, and potentially higher resale values. Prospective homeowners should carefully evaluate their long-term priorities and financial plans to determine which construction type aligns best with their goals.
Average Costs per Square Foot for Multifamily Construction in California
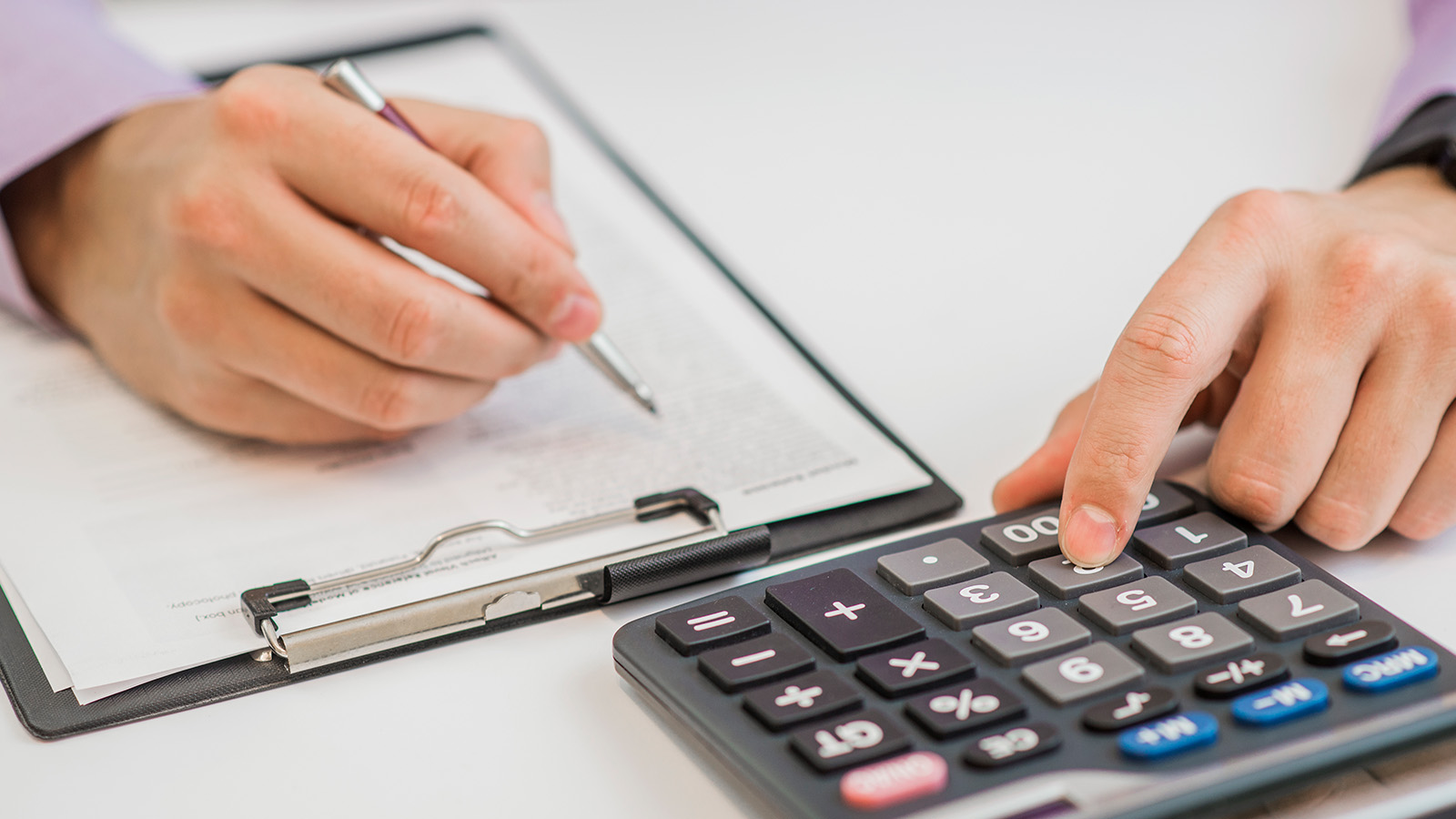
The cost of constructing multifamily buildings in California also varies based on factors such as location, site conditions, design, materials, and labor. As of recent data, the average construction cost for multifamily properties in the United States is approximately $350 per square foot. However, in major California markets like San Francisco and Los Angeles, costs are significantly higher. For instance, San Francisco's construction costs have been reported at $473 per square foot, ranking it among the most expensive cities globally for building. Los Angeles also experiences elevated costs, though specific figures may vary.
Factors Influencing Construction Costs
Several factors contribute to the high costs associated with Type III multifamily construction in California:
- Increased Demand: California faces a persistent housing shortage, with an estimated deficit of 3-4 million housing units as of 2017. This shortfall has intensified demand for new residential construction, leading to increased competition for available resources and, consequently, higher costs. Wikipedia
- Tariffs on Building Materials: Trade policies have a direct impact on construction expenses. Proposed tariffs, such as a 25% levy on imports from Canada and Mexico, could significantly raise the cost of essential building materials like lumber and steel. Given that the U.S. imports a substantial portion of these materials from its neighbors, such tariffs are expected to exacerbate the housing affordability crisis by inflating construction costs. The Guardian
- Labor Shortages: The construction industry in California is experiencing a labor shortage, partly due to restrictive immigration policies and competition from other sectors. This scarcity drives up labor costs, as developers must offer higher wages to attract skilled workers. The situation is further strained by the need to rebuild after natural disasters, such as wildfires, which divert labor resources to affected areas. San Francisco Chronicle
Projected Increases in Construction Costs
The convergence of high demand, tariffs, and labor shortages is projected to escalate construction costs further. For example, construction costs in California increased by approximately 25% between 2010 and 2020, with significant contributions from rising material and labor expenses, as well as the pandemic. Post-pandemic we saw pricing stabilization, but not a return to pre-pandemic construction costs. The introduction of new tariffs could exacerbate this trend, leading to even higher costs in the coming years.
It’s important to note that we’re primarily talking about exterior wall ratings here, and your roof is a key element in your building envelope. In Type III construction your roof may only have a 1-hr fire rating. Letter Four would like to consider upgrading that rating to 2-hours for a consistent level of fire resistance around the entire building. Check out this blog for more information.
Why Choose ICF Construction in Los Angeles?
We mentioned ICFs above, now let’s take a deeper dive into this option. ICFs offer several advantages over traditional wood-framed construction, particularly in terms of fire resistance, durability, and compliance with Type III construction requirements.
1. Superior Fire Resistance
One of the primary reasons to consider ICF construction in Los Angeles is its exceptional fire resistance. The solid concrete core provides a fire-resistance rating of up to 4 hours, far exceeding the 2-hour rating required for Type III construction. In contrast, wood-framed homes burn quickly and can collapse in as little as 30 minutes during a fire event.
- ICF walls do not burn, preventing the spread of flames.
- The polystyrene insulation used in ICFs melts away at high temperatures but does not contribute to combustion.
- With the appropriate exterior finishes, ICF homes can achieve a zero flame spread rating.
Given that Los Angeles has upgraded many areas to Very High Fire Hazard Severity Zones (VHFHSZs) in recent years, adopting fire-resistant construction materials is a critical step in safeguarding homes.
2. Energy Efficiency and Sustainability
ICF homes significantly outperform wood-frame homes in energy efficiency due to their high thermal mass and insulation properties.
- The continuous insulation eliminates thermal bridging, reducing heating and cooling costs.
- Homeowners can expect up to 50% energy savings compared to wood-frame homes.
- ICF walls contribute to reduced carbon emissions by lowering HVAC energy consumption.
California has some of the highest electricity rates in the country, making energy-efficient construction essential. ICF homes help homeowners save on utility bills while contributing to sustainability goals.
3. Strength and Disaster Resilience
Beyond fire resistance, ICFs offer superior strength against natural disasters, including earthquakes, high winds, and floods.
- Earthquake Resistance: ICF structures exceed seismic building code requirements because reinforced concrete provides excellent structural integrity and flexibility.
- Wind and Storm Resistance: ICF homes can withstand hurricane-force winds up to 250 mph, making them highly durable against extreme weather.
- Pest and Mold Resistance: Unlike wood, concrete does not rot, mold, or attract termites, reducing long-term maintenance costs.
Meeting Type III Construction Requirements with ICF
Los Angeles building codes require Type III construction for certain residential and multifamily developments. This classification mandates non-combustible exterior walls with a minimum 2-hour fire-resistance rating. ICF construction not only meets but exceeds these requirements.
- Concrete core thickness determines fire rating: A 6-inch ICF wall typically achieves a 3- to 4-hour fire rating.
- Approved by Los Angeles Building Codes: The City of Los Angeles Department of Building and Safety (LADBS) recognizes ICF as an approved construction method for meeting fire and seismic code requirements.
For verification, homeowners and builders should consult with local officials and refer to resources such as the International Code Council (ICC) for evaluation reports on ICF fire-resistance compliance.
Cost Considerations: ICF vs. Traditional Wood-Framed Construction
One common misconception is that ICF construction is prohibitively expensive compared to traditional wood framing. While initial material costs may be higher, ICFs provide significant long-term savings through reduced maintenance, lower insurance premiums, and energy efficiency, much like CMU construction.
The cost difference between building a single-family home in California using Insulating Concrete Forms (ICF) versus traditional wood-frame construction varies based on several factors, including material prices, labor costs, and regional considerations. Historically, ICF construction has been approximately 5% to 15% more expensive than wood-frame construction. For instance, a study by the U.S. Department of Housing and Urban Development indicated that ICF construction could add about 3% to 5% to the total purchase price of a typical wood-frame home.
However, fluctuations in material costs can influence this difference. For example, during periods of high lumber prices, the cost gap between ICF and wood-frame construction may narrow, making ICF a more competitive option. Conversely, when lumber prices are stable or low, the cost difference may widen.
It’s essential to consider that these figures are averages and can vary based on specific project requirements, local labor rates, and material availability.
While ICF homes may cost 5-15% more initially, this premium is offset by long-term savings on insurance, energy bills, and maintenance.
Insurance Savings
Since ICF homes are far more fire-resistant than wood-frame structures, homeowners often see insurance premium reductions of up to 50%. Given the increasing wildfire risks in California, insurers are raising premiums for wood-frame homes in high-risk zones.
Long-Term Savings
- Energy savings: Up to 50% lower utility bills due to improved insulation.
- Minimal maintenance: Concrete does not rot, mold, or attract termites, reducing costly repairs.
- Resale value: Fire-resistant and disaster-resilient homes hold higher property values.
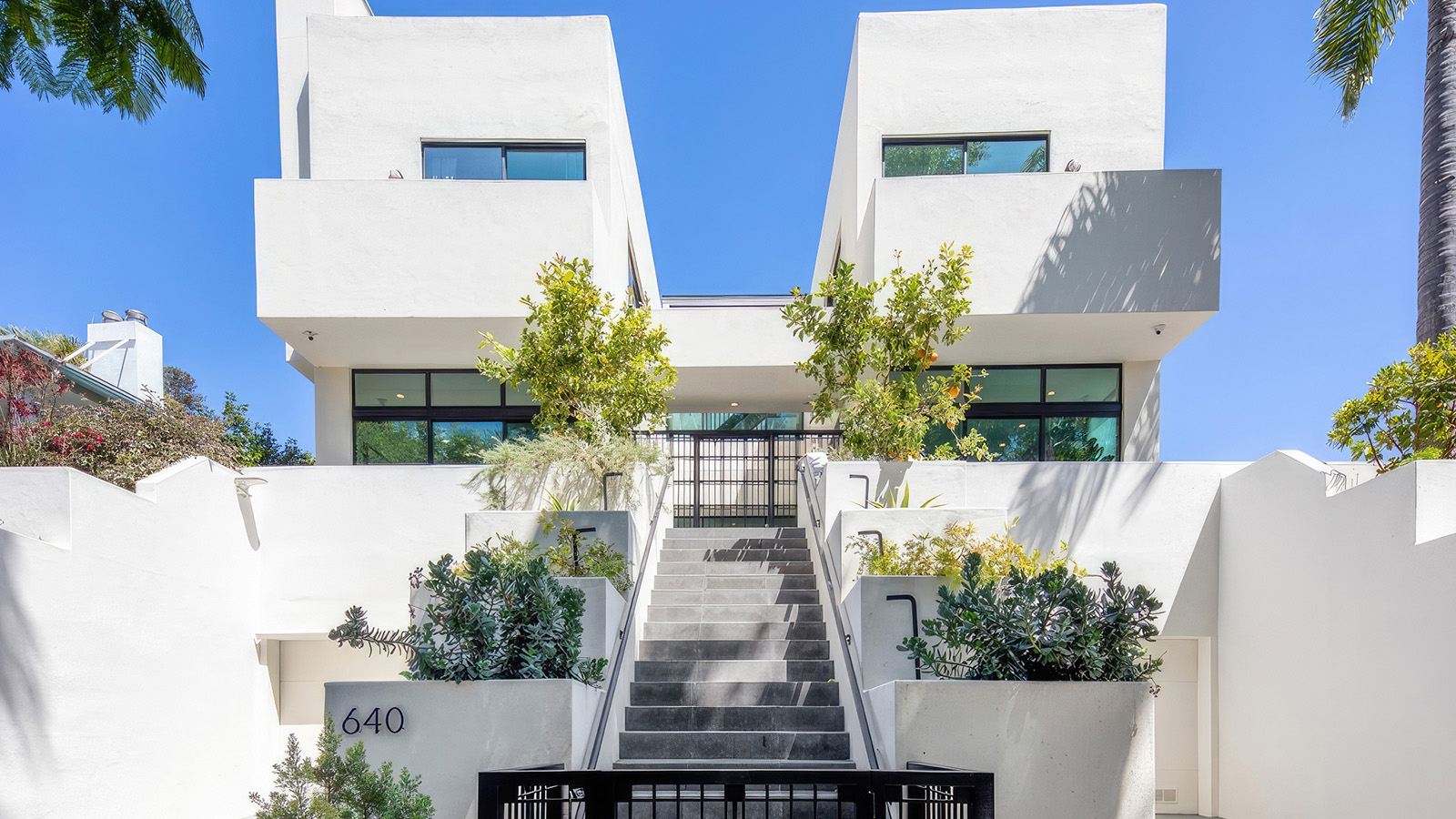
ICF Availability: Are There U.S. Manufacturers?
To further control costs and reduce tariff-related price increases, California can prioritize U.S.-made ICF products. Several American companies manufacture high-quality ICF blocks, including:
- Fox Blocks (foxblocks.com)
- Nudura (nudura.com)
- Amvic (amvicsystem.com)
- Logix ICF (logixicf.com)
By sourcing materials domestically, builders can avoid import tariffs on foreign materials, lowering overall project costs.
Challenges to Widespread Adoption of ICF in Los Angeles
Despite its advantages, ICF construction still faces barriers to widespread adoption, including:
- Limited Contractor Familiarity: Many builders and subcontractors in California have more experience with traditional wood framing. Training and certification programs can help bridge this knowledge gap.
- Perceived Higher Costs: While ICF is slightly more expensive upfront, education on life-cycle savings is needed to encourage adoption.
- Code and Permitting Adjustments: While ICF is approved by LADBS, some local municipalities may have additional permitting requirements, requiring further advocacy for streamlined approvals.
How Can Los Angeles Promote ICF Construction?
To encourage ICF adoption, the City of Los Angeles can implement incentives and regulatory adjustments, such as:
- Fire-Resistant Housing Incentives: Tax credits or rebates for homeowners who choose ICF in fire-prone areas.
- Insurance Discounts for Fire-Resistant Homes: Collaborating with insurance companies to offer greater premium reductions for ICF homeowners.
- Expedited Permitting for ICF Homes: Faster approval processes for fire-resistant structures.
- Contractor Training Programs: Partnering with organizations like the American Concrete Institute (ACI) to provide ICF-specific training.
Conclusion
As California continues to battle increasingly severe wildfires, fire-resistant construction should become the new standard for single-family homes in Los Angeles. Whether it’s CMU block construction or ICFs, as architects and builders we need to provide a solution that offers superior fire resistance, energy efficiency, and disaster resilience compared to traditional wood-framed construction.
Letter Four’s truly in-house Design-Build model is uniquely suited to help homeowners rebuild Los Angeles with greater efficiency, responsible and experienced budget development, and design cohesion. By seamlessly integrating architecture, interior design, and construction under one roof, Letter Four eliminates the disconnect that often occurs between designers and builders, ensuring that each project stays on budget, on schedule, and aligned with the homeowner’s vision. This holistic approach is particularly valuable in rebuilding efforts after wildfires and natural disasters, where coordination, speed, and adherence to evolving fire-resistant building codes are essential. With expertise in fire-resilient materials, streamlined permitting, and sustainable and Passive House construction, Letter Four is not just restoring homes but helping shape a stronger, safer, and more resilient Los Angeles.
Book a call today to discuss how we can help you to rebuild your home and your life.